Process mining reveals bottlenecks in your operations and makes your teams more efficient
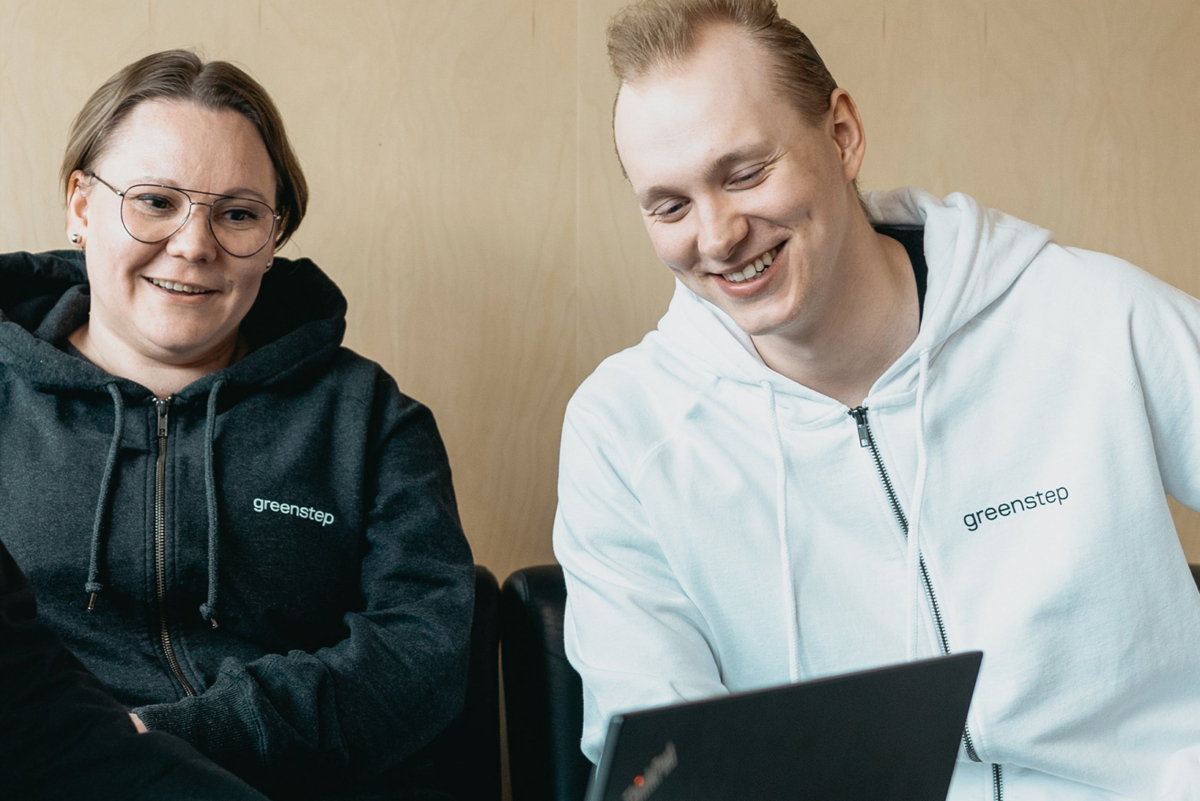
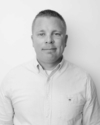
Simo Parkkali
Sales Director
The common goal of corporate operational managers, team leaders and virtual team leaders is to create an environment and operating models where everyone can do their jobs as efficiently and smoothly as possible.
However, in terms of actual operations, or processes, team boundaries are blurred and the delivery of outputs requires multiple and different flows of information across and around these team boundaries. Even a single piece of incomplete or incorrect information can cause chaos, clarification and other deviation procedures that take time away from the actual work and thus reduce the team's performance.
It is
often these processes that offer the greatest potential for improving
performance - the ability of employees to carry out their tasks smoothly
without additional disruption. Process mining effectively uncovers these
anomalies, disruptions and bottlenecks so your team can focus on what matters
most.
Know, what to optimize
Before you can start optimising, let alone automating, the process, you need to understand what kind of entity you are dealing with. This understanding is often aided by some form of process description, i.e. visualisations of the process flow, steps, responsibilities and other essential details. The description can also be a verbal document, but a visual image is usually more practical and easier to internalise. For example, have you ever tried to assemble furniture using only verbal instructions?
The downside of describing processes, however, is that it often becomes a rather heavy, challenging and time-consuming task. Describing a process requires the input of several people to ensure that all the different steps and responsibilities are described accurately and correctly. On top of this, interviews with experts, review of often outdated documents, workshops on imaging and other time-consuming methods do not necessarily reveal all the interesting variations. The end result is a process picture that looks straightforward and competent, but does not reflect the real world.
Bringing process mapping into the 2020s
Process mining has brought process mapping into the present day. Automated Process Discovery (APD), can be performed from event logs in information systems and provides immediate visibility to identify the first bottlenecks.
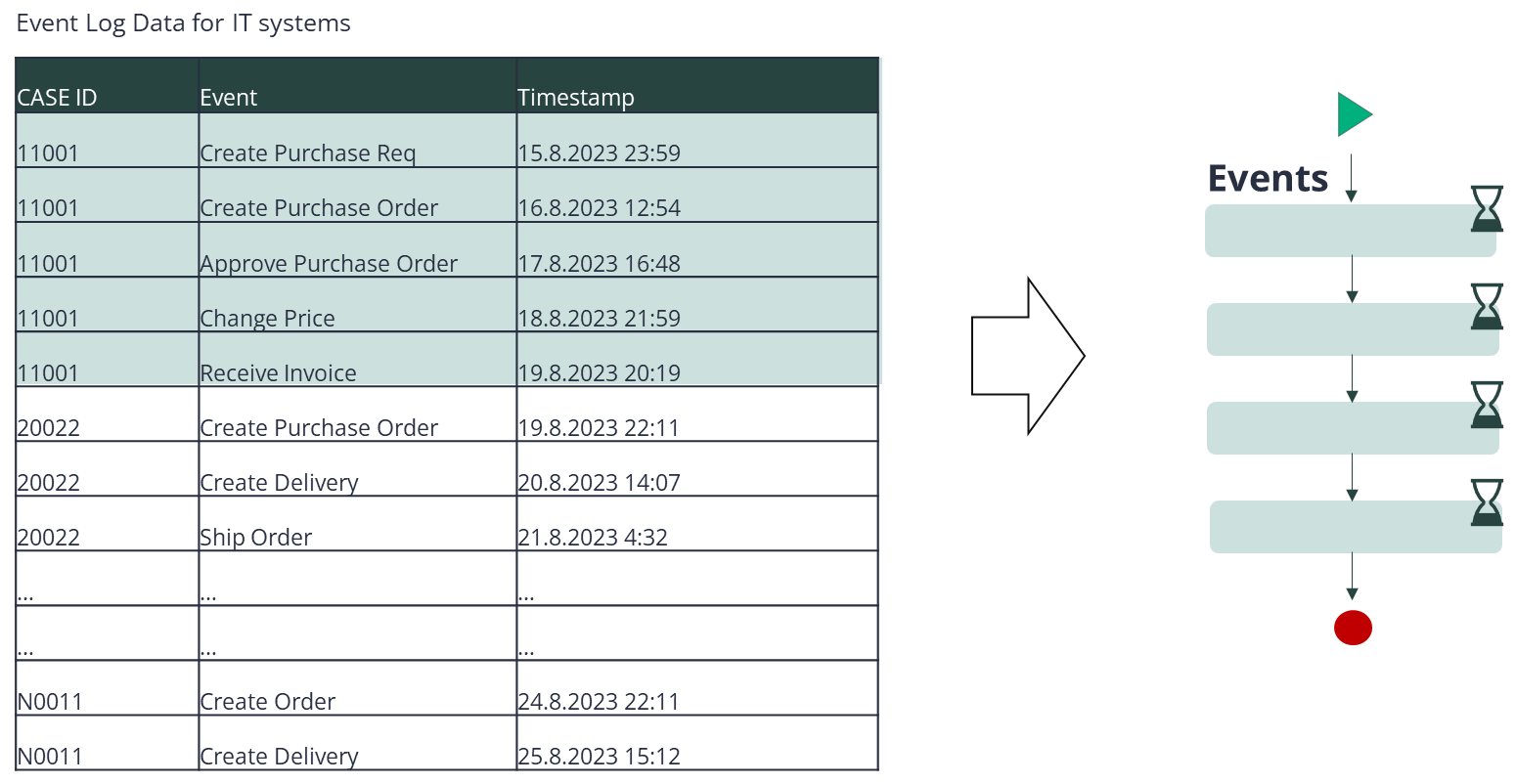
The use of event logs not only makes process imaging automatic, but it also makes it much more accurate than previous, highly subjective, imaging methods. Process mining models an image of each process variation and accounts for every deviation that may have affected the process workflow along the way. Process mining provides a completely objective picture of the real world as things really happened. The process model can be updated automatically, so it is always up to date.
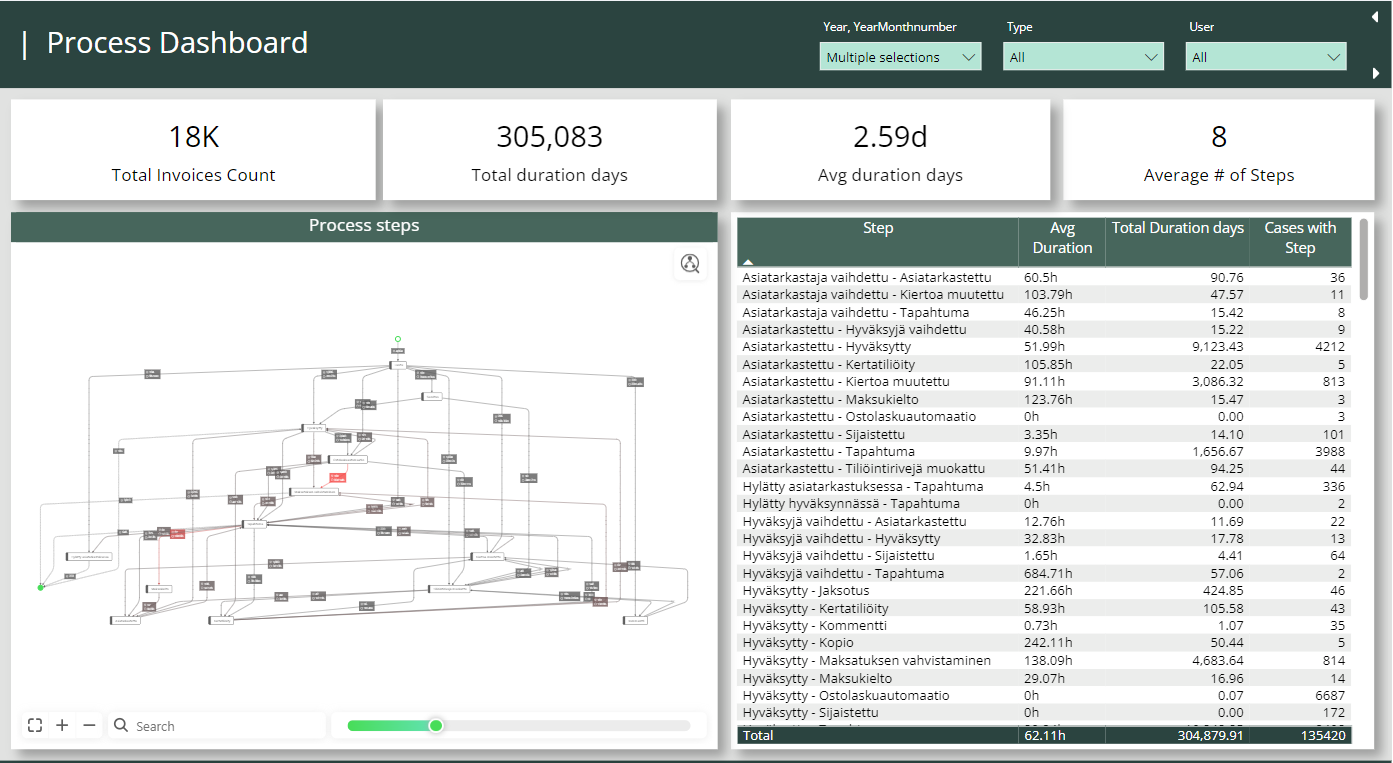
Process Tracking gives management, front-line staff and other process developers a clear picture of development needs without time-consuming pre-screening. The valuable input of experts can be focused on target state planning, and the enthusiasm for development is not lost in the early stages.
Published 23.10.2023